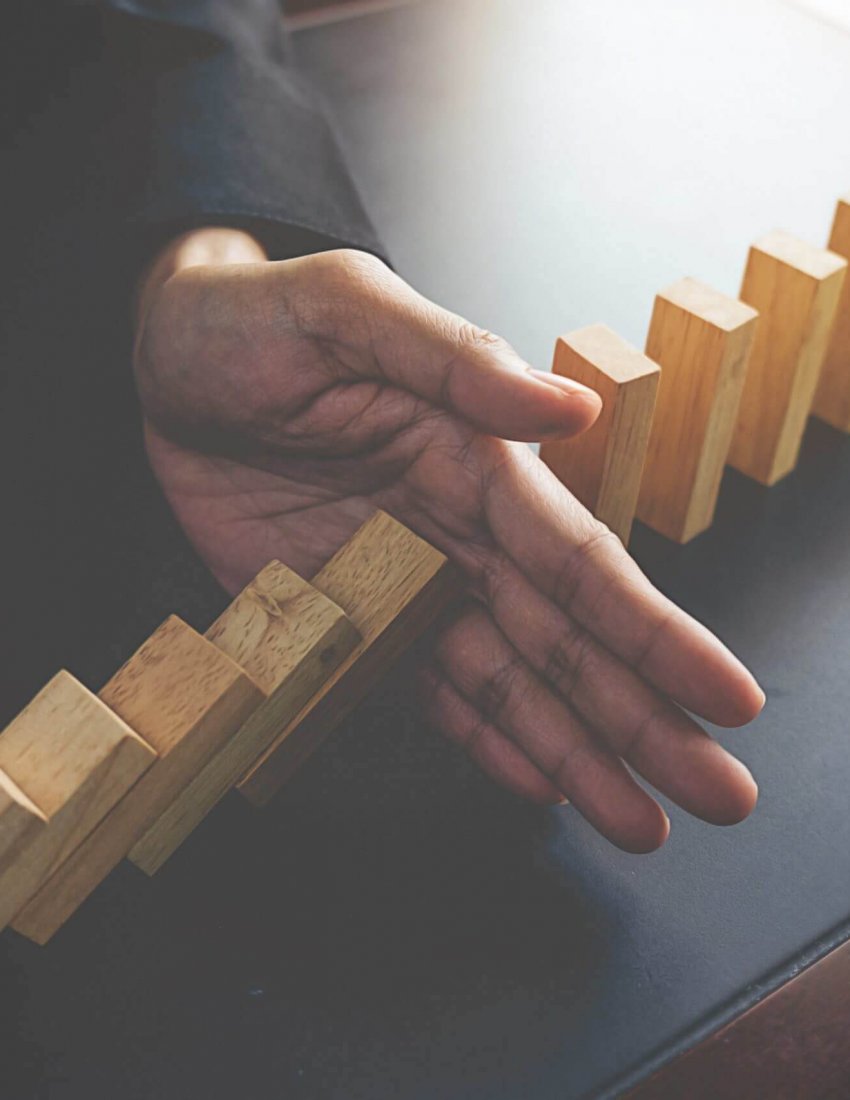
La chaîne numérique, en avez-vous déjà entendu parler ?
En s’installant progressivement dans les usines, le développement informatique a offert de nouveaux outils aux industriels afin de booster la productivité : interconnexion des chaines de production, échange d’information en temps réel entre l’atelier et les services support (bureau d’études, méthodes, contrôle…).
Désormais, l’évolution numérique n’est plus une option mais une obligation pour les entreprises industrielles qui veulent croître dans les années futures.
Découvrez donc dans cet article les enjeux de la chaîne numérique et de l’usine 4.0.
L'usine 4.0 et l'enjeu de la chaîne numérique
L’industrie se tourne depuis plusieurs années vers de nouvelles technologies, sources de productivité. De l’usine dite « classique », nous voyons apparaître des usines modernes, plus intelligentes et connectées, en adéquation avec l’évolution de la société.
33,5% des directeurs d’entreprises industrielles considèrent le numérique comme un levier de croissance, selon l’étude « Baromètre de la transformation numérique » réalisée par l’Usine Nouvelle en 2014. Le numérique s’immisce également dans les services techniques de l’entreprise. En effet, plus de 60% des répondants pensent que le numérique permet de développer la compétitivité des services du Bureau d’Etudes, des Méthodes et de la Production.
L’entreprise se dirige donc vers une automatisation croissante de ses process. Le numérique s’impose aujourd’hui comme l’une des évolutions majeures des entreprises industrielles. La chaîne numérique en est d’ailleurs un élément central.
A découvrir également : “7 étapes pour dynamiser votre croissance”.
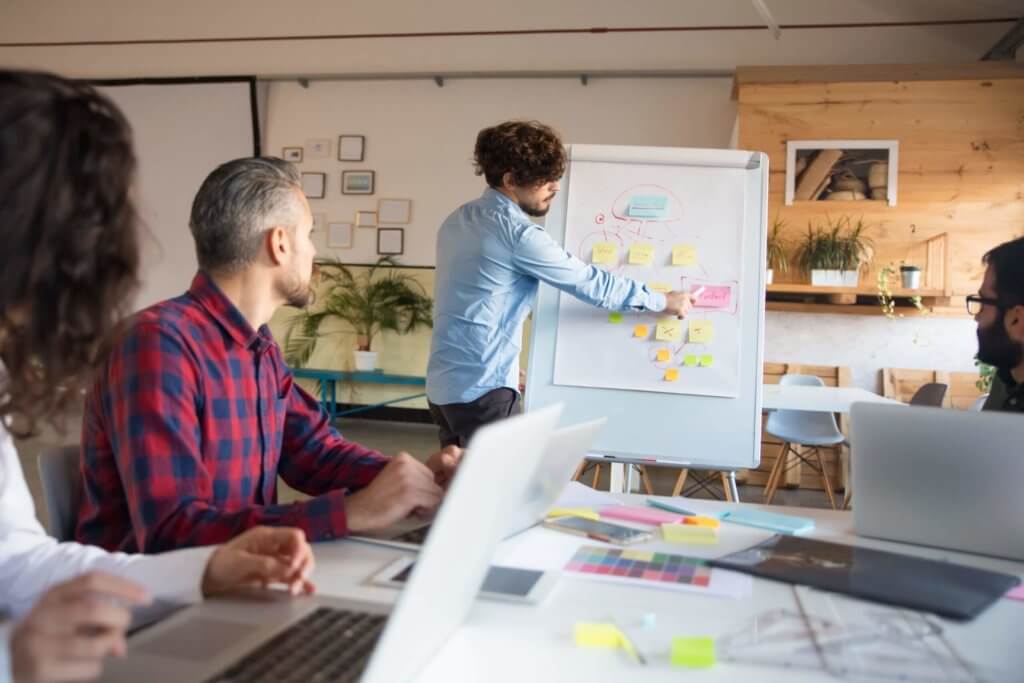
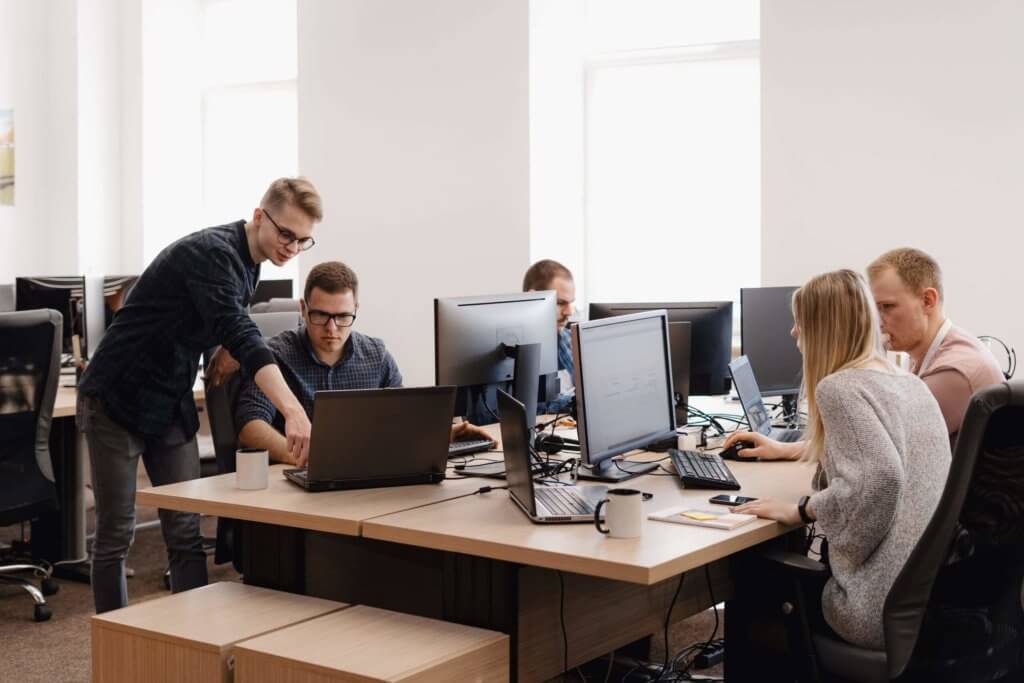
Qu'est-ce que la chaîne numérique ?
Le principe de la chaîne numérique consiste à contrôler numériquement les flux d’information, de la conception du produit jusqu’à sa fabrication. Elle créée un lien direct entre différents outils informatiques afin qu’une information fiable soit diffusée à tous les services de l’entreprise.
Auparavant cloisonnés et trop segmentés, ces services s’organisent désormais autour d’un travail collaboratif. Le but étant d’améliorer le « Time to Market » : l’enjeu majeur des entreprises industrielles.
L’objectif de la chaîne numérique est de permettre aux services Bureau d’Etudes, Méthodes et Production de mieux communiquer et de contrôler les flux de données tout au long du processus d’industrialisation d’un produit.
Les gains à attendre de la mise en place d’une chaîne numérique complète sont nombreux.
L’instauration d’un process de fonctionnement global permet la répétabilité des opérations et la fiabilisation des données. Ainsi, les erreurs dues aux ressaisies sont éliminées et le nombre de modifications à réaliser décroit également. Une gestion en temps réel qui augmente de manière significative la réactivité des différents services concernés et améliore ainsi leur communication.
Le principe de la chaîne numérique et son application industrielle
Une pièce manufacturée passe par une succession d’étapes de sa conception à sa fabrication. Nous pouvons les regrouper sous la terminologie de PLM (Product Lifecycle Management) pendant lesquelles le recueil d’une information fiable est indispensable.
L’élaboration de ce processus industriel va faire intervenir une multitude de logiciels : CAO, PDM, FAO, ERP, MES etc. Leur maîtrise par les différents opérateurs est nécessaire afin d’assurer une conformité totale à la pièce.
Tout l’enjeu de la chaîne numérique est de rendre interdépendant l’information. Cela va des spécifications techniques (désignation, dimensions, temps, prix), jusqu’au plan et à leur indice au travers de ces systèmes d’informations hétérogènes. L’intérêt étant d’optimiser l’ensemble des flux de la société (Vente, Achat, Production).
Exemple d’une chaîne numérique complète :
Prenons l’exemple d’une pièce X qui passe par différents logiciels. A chaque étape, les informations se déplacent de manière dynamique et instantanée entre les logiciels, de manière descendante et ascendante.
Etape 1 : la conception CAO par le Bureau d'Etudes
Tout commence au Bureau d’Etudes, qui réalise une conception 3D sur un logiciel de CAO, en fonction d’un cahier des charges. Les données techniques (code article, indice, nomenclature…) sont définies et transitent vers l’ERP.
Etape 2 : la mise à disposition des données à travers l'ERP
L’ERP recueille l’ensemble des données du Bureau d’Etudes et les met à disposition des services Méthodes. Ces services viendront ensuite industrialiser la fabrication de la pièce par l’adjonction de gammes de fabrication.
L’ensemble des plans peut être aussi récupérer ainsi que leurs indices. Les modifications ultérieures réalisées par le Bureau d’Etudes sont alors mises à jour directement dans l’ERP.
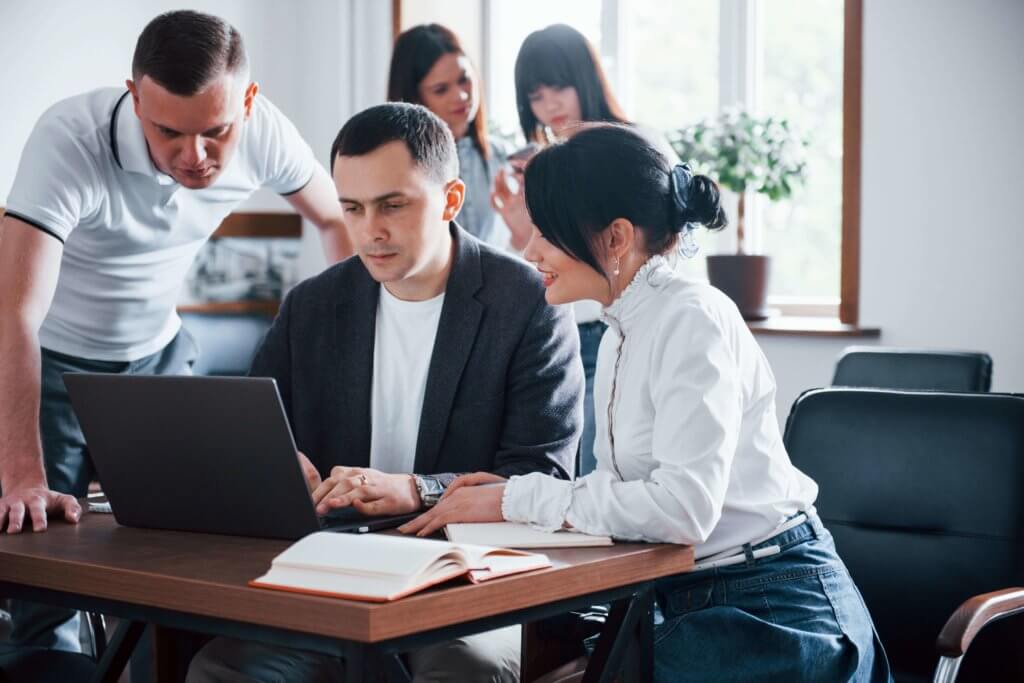
C’est le cas de l’ERP Open Prod qui récupère en automatique (ou manuellement) les nomenclatures et indices de plan grâce à son lien natif avec différents logiciels de CAO. Cela est notamment le cas avec Solidworks de Dassault Systèmes, leader sur le marché français.
Etape 3 : la préparation de la production
Le cas échéant, le service Méthodes intervient alors pour déterminer l’usinage à appliquer à la pièce. Il créer également les programmes destinés aux machines à commandes numériques au travers d’un logiciel de CFAO.
L’ERP transmet la liste des besoins (issue du carnet de commande) et l’ensemble des informations techniques (dimensionnelles) au service Production afin de pouvoir réaliser les lancements adéquats en production.
Etape 4 : l'interaction de tous les services de l'entreprise
En parallèle, tous les services de l’entreprise « agissent » grâce aux données transmises instantanément à l’ERP.
- Notamment le service Achats qui peut lancer les approvisionnements pour réaliser les commandes et livrer à l’heure. Cela est possible dès que la nomenclature est injectée depuis la CAO et qu’elle a été validée par le service Méthodes. Ce qui est particulièrement vrai dans le monde de la machine spéciale où les délais d’approvisionnement sont souvent longs et nécessite une anticipation et une gestion accrue.
- Dans l’atelier, le système MES (Manufacturing Execution System) remonte, en temps réel, les informations liées aux machines et aux opérateurs (temps de production, consommations, pièces produites…). Cela permet un pilotage affiné de la production afin de calculer les prix de revient et l’efficience de l’atelier.
En conclusion...
On peut résumer la mise en place d’une chaîne numérique complète dans une entreprise industrielle comme la somme de toutes les suppressions des tâches de ressaisies et/ou de faible valeur ajoutée, liées aux process de conception, d’industrialisation et de production des pièces manufacturées.
Les gains de productivité peuvent être considérables tant en termes structurels, organisationnels, financiers et qu’en termes d’image par une augmentation générale des taux de services.
